Saw Blade Tech
Learn about blade configurations
All EAB blades are designed to produce optimal results. A bit of blade knowledge, however, can help you choose between similar blades, and understand the benefits of keeping a selection of blades in your toolbox.
CARBIDE GRADE
EAB tungsten carbide is rigorously tested and graded:
- C2 to C4 for wood-based construction materials
- C6 for metals and Poly Crystalline Diamond (PCD) for fiber cement products
Generally speaking, the higher the grade the harder the tooth, which results in a sharper edge and longer life. However, harder carbide is more brittle and more easily damaged. Blades used for framing and general construction tend to use C2 and C3 carbide which is more shock resistant.
HOOK ANGLE
The hook angle is the amount of forward or backward lean of each tooth. Generally speaking, a higher hook angle will give you an aggressive cut and a fast feed rate. EAB RazorBack blades have a very aggressive 27° hook for ultra-fast, controlled cutting. A low or negative hook (less than 5°) produces a smoother, slower cut, and is ideal for hard and brittle materials such as melamine and metal. Negative hook angles also inhibit the blade’s tendency to climb the material being cut, which is why they’re a must for use on miter saws and radial arm saws.
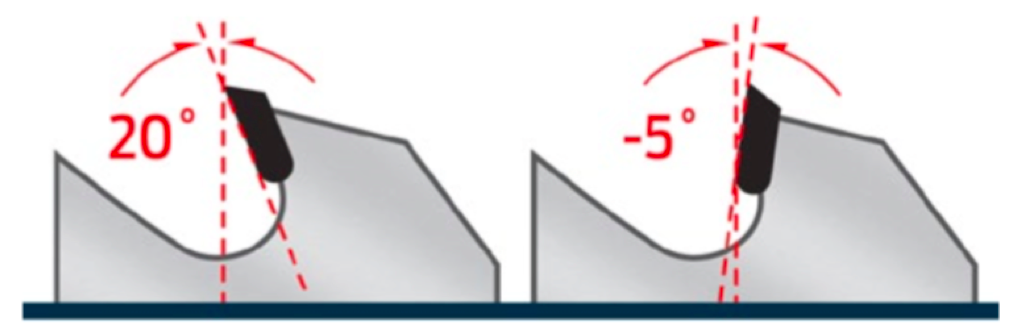
GENERAL CARBIDE BLADES
EAB general (GEN) carbide blades are designed for general purpose ripping and cross cutting of wood and composite materials and are a top choice for light and medium duty work. Our decking and shelving blades are tipped with superior quality C2 tungsten carbide, have hard plates (HRC-40), expansion slots, and are sharpened on the top, face and sides. Blades 10” and up also have tension rings for improved flatness.
PROFESSIONAL CARBIDE BLADES
These blades are made from top quality hardened steel (HRC-40+) and are brazed with superior quality tungsten micrograin carbide teeth that are ground on the face, top and sides with a fine 600 to 1,000 grit diamond wheel to achieve maximum sharpness. They have expansion slots, and blades 10” and up have tension rings for improved flatness. These blades are designed for heavy duty use and are the top choice of professionals.
INDUSTRIAL CARBIDE BLADES
The ultimate blade series, designed for the continuous heavy duty applications. Manufactured with top quality, hardened SKS plate, and brazed with superior quality micrograin carbide teeth, which are fully sharpened with a super fine 1,000 grit diamond wheel to achieve maximum sharpness. These blades have laser cut bodies, expansion slots and tension rings for improved flatness and continuous heavy duty usage. This line of blades also includes specialty blades not normally available to the retail customer.
NUMBER OF TEETH
A good rule of thumb, regardless of the blade’s diameter or thickness of the material, is to have 2 to 4 teeth in the material you’re cutting. This will give you the smoothest cut, optimal chip removal, and the least amount of friction and strain on your equipment—it’s also safer.
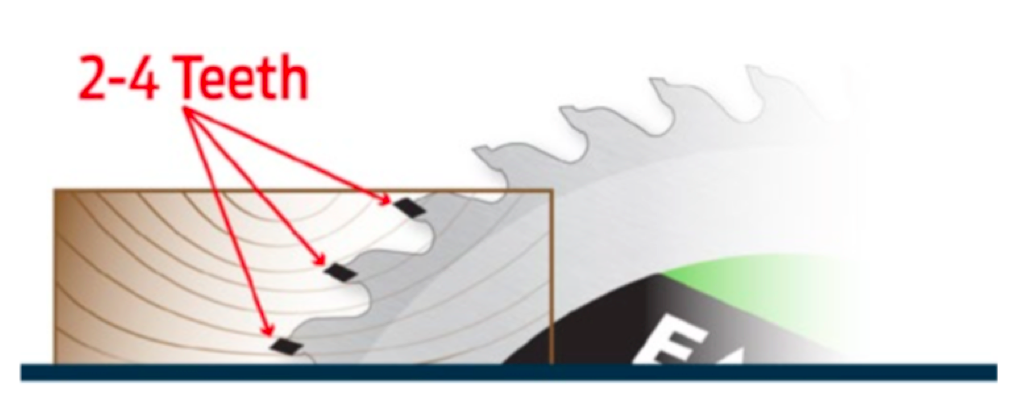
TOOTH CONFIGURATION
The design of a blade’s teeth determines how well it will cut different materials.
![]() |
Alternate Top Bevel (ATB)ATB is the most common tooth configuration for cutting wood and wood-based materials. Teeth alternate between right and left-hand bevels, to alternately slice through the material’s fibers for fast, smooth cutting. |
![]() |
Alternate Top Bevel with Raker (ATBR)Found on our All Purpose blades designed for crosscutting and ripping. Teeth are arranged in groups of five — four ATB teeth and one flat top raker tooth — with a large gullet between the groups to remove larger chips when ripping. This configuration is also known as planer combination. |
![]() |
Triple Chip Grind (TCG)For cutting hard, solid materials such as MDF, plastics, laminates and non-ferrous metals. Teeth alternate between a flat raking tooth and a higher chamfer tooth, which produce very clean cuts, though at a much slower feed rate. |
![]() |
High Alternate Top Bevel (Hi-ATB)For extra-fine crosscutting and for materials prone to chipping, such as melamine, hardwood and laminate flooring and fine hardwoods. The high bevel accentuates the razor sharp slicing action at the edge of the blade and provides a sandpaper smooth finish. Found on our PRO and IND Razor Tooth ultimate finishing blades. |
Stay safe when operating power tools
Always operate power tools according to manufacturer’s instructions, never exceed a blade’s maximum RPM, and use appropriate protective gear and clothing. For more information about safety symbols and what they mean, visit our glossary.
Learn more about selecting the right blade for you and your job.
Start your search now for the right blade for your job.